Manufacturers and workers needed a location to produce the goods that people would need on a regular basis, thus factories were established. Examples include supplying a plant that makes automobiles and motorcycles with food, clothing, and home items. Factories are the lifeblood of every nation’s economy, and modern factories run on automated systems that rely on parts like omron automation component Malaysia.

Basic understanding of what a factory automation system is
The term “factory automation” refers to the practice, prevalent in the manufacturing industry, of increasing production while simultaneously cutting costs through the utilization of automated machinery and computer systems. It is feasible to completely remove the need for any kind of human involvement in a process by automating every step of it, from the smallest component to the entire thing.
There are no restrictions placed on the parts of the plant that may be automated, beginning with the processing of raw materials and continuing all the way through the packaging and shipping of final products.
The Available Types Of Factory Automation Systems
When it comes to manufacturing, the degree of automation will vary depending on a number of things including the nature of the process, the availability of resources, and so on. Most industries have adopted some form of automation.
Automated Production Lines
Each workstation on an automated production line has a distinct purpose in the overall manufacturing process, and the two main components of an automated production line are the conveyor system and the individual workstations.
The amount of human intervention is directly proportionate to the level of automation, and the steps involved are clearly laid out. In a completely automated line, the only tasks performed by humans are those of supervision, monitoring, adjusting, and maintaining the machinery.
Fully Automated (End-To-End)
In an ideal world, factories would be totally automated from beginning to end, eliminating the need for human labour and allowing for continuous production at all hours of the day and night. These factories may have features like self-regulation and quality control checks on their wares.
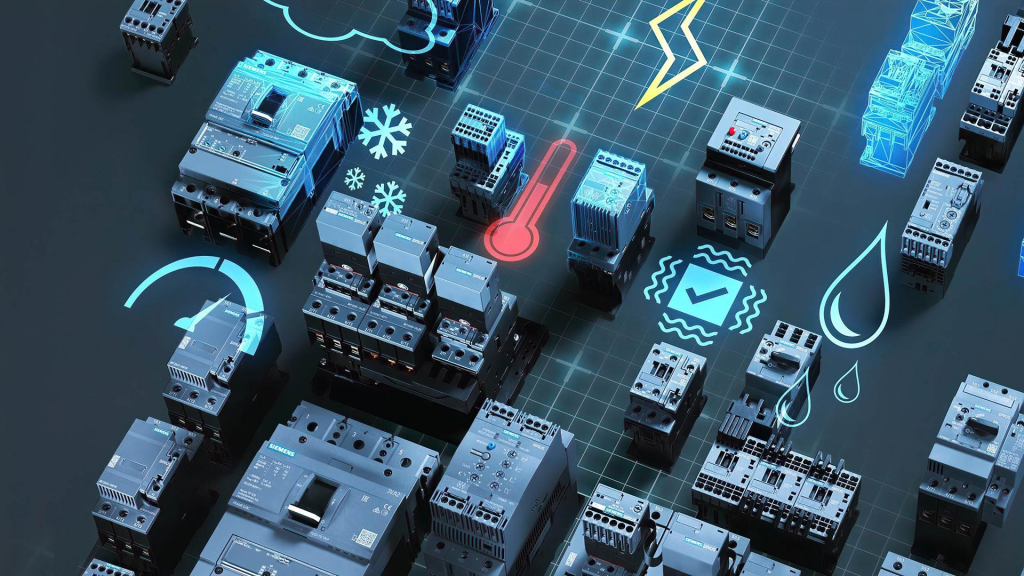
What are the main components of industrial automation?
PLC (Programmable Logic Controller)
Continuously analysing the condition of input devices and making decisions to control the state of output devices based on a bespoke programme, a Programmable Logic Controller (PLC) is a type of industrial control system. A PLC is a programmable logic controller that may be used to automate a process or machine by sensing inputs, evaluating those signals, and adjusting the machine’s or process’s outputs accordingly.
Distributed Control System (DCS)
A Distributed Control System (DCS) refers to a control system for a manufacturing facility that uses many independent controllers located in different parts of the system.
Better strategies for enhancing control stability, process quality, and plant efficiency have emerged as a result of the decentralised nature of the plant’s control system architecture.
SCADA
The term “supervisory control and data acquisition” (SCADA) refers to a control system architecture that utilises computers, networked data transfers, and graphical user interfaces to keep tabs on machinery and processes at a high level. This operation might be factory, infrastructural, or facility-based. Industrial operations, such as production, power generation, manufacturing processes, and refining, can operate in either a continuous, batch, repetitive or discrete mode.
Public or private organisations may engage in infrastructure operations such as water and sewage treatment, garbage collection and disposal, oil and gas pipelines, power transmission and distribution, and other similar tasks.