Even the tiniest portion of a mechanism can have an impact on the machine’s daily operation. When it comes to the mechanisation of all of these components, the machining center’s technology and quality are critical. As a result, investing in the most up-to-date CNC lathes (Computerized Numerical Control) is the greatest way to get high-precision, reliable parts in a short amount of time. Do you want to learn more about component machining? Do you have reservations about machining companies? This is a must-read article.
Manufacturing industries are working in a considerably more flexible manufacturing environment as a result of technological advancements and the high competitiveness of industrial marketplaces. This progress necessitates faster project development and utmost precision in each of its components. All of this was done with one goal in mind: to avoid delays and cost overruns.
If you work as a project manager or in buying, you understand the importance of selecting a reliable machining firm. Its selection can help your prototype succeed, as well as the start-up or production of your project. In this content, here are some methodological notions that will assist you in your daily job.
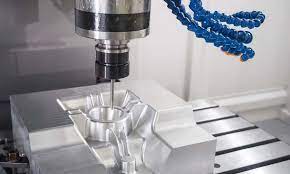
What should you remember when selecting a machining company?
Practical technology for mechanization
There are a plethora of options available, all of which are more or less cost-effective and of varying quality. Before you begin, you must be extremely clear about your company’s or project’s requirements: piece shape and dimensions, number of required pieces, equipment (drills, blades, cutters), number of ideal axes for machining, number of turns they can handle, and so on.
In terms of technology, three categories can be divided:
Chip removal during machining: The part’s material is removed or cut using a precision tool here, resulting in waste or chips. The biggest issue with this technology until recently was obtaining small bits by cutting. Injection-based systems can now produce parts as small as 10gr with far greater precision and homogeneity than other traditional methods.
Machining without the removal of chips. Synthesized, lamination, stamping, and casting are some of the metal forming procedures used here. If you want the optimal relationship between precision and manufacturing speed, this is not an operational option.
Abrasion or EDM machining. In this situation, the extra material is removed using a revolving disc or grinding wheel that rotates at a high cutting speed, separating microscopic particles. They get excellent precision but require a lot of uptime.
Apart from this precision machining Malaysia technology, you can learn about 3D printing, one of the latest developments. This solution is capable of designing a part in a very few hours. Despite this, the laminated finish of the pieces designed by 3D, as well as their limitation in terms of materials and compatibilities, do not make them suitable for any application.